How to Improve Biochar Pyrolysis Reactor Efficiency
- arbourz
- Mar 2
- 4 min read
Maximizing the efficiency of a biochar pyrolysis reactor is critical for optimizing product yield, reducing energy consumption, and improving the overall economic viability of biochar production. The pyrolysis process, which thermally decomposes biomass in an oxygen-limited environment, requires precise control over various operational parameters. Efficient reactor design, optimized feedstock preparation, and effective energy utilization are key factors that influence reactor performance.
Optimizing Reactor Design
The structural and functional configuration of a biochar pyrolysis reactor directly affects conversion efficiency and product distribution. Modern reactor designs incorporate several enhancements to improve thermal efficiency and product yield.
Continuous vs. Batch Systems: Continuous reactors, which facilitate a steady flow of biomass feedstock, offer superior efficiency compared to batch reactors. They allow for sustained heat utilization, reducing thermal losses and improving overall process stability.
Heat Recovery Mechanisms: Incorporating heat exchangers and secondary combustion units can capture excess heat from the pyrolysis process and redirect it to preheat incoming biomass. This minimizes external fuel requirements and improves the reactor’s thermal efficiency.
Residence Time Control: Fine-tuning the residence time of biomass within the reactor ensures optimal thermal degradation. Shorter residence times favor syngas production, while prolonged exposure at moderate temperatures enhances biochar yield. Automated control systems can regulate biomass feed rate and heating duration to maintain desired process conditions.
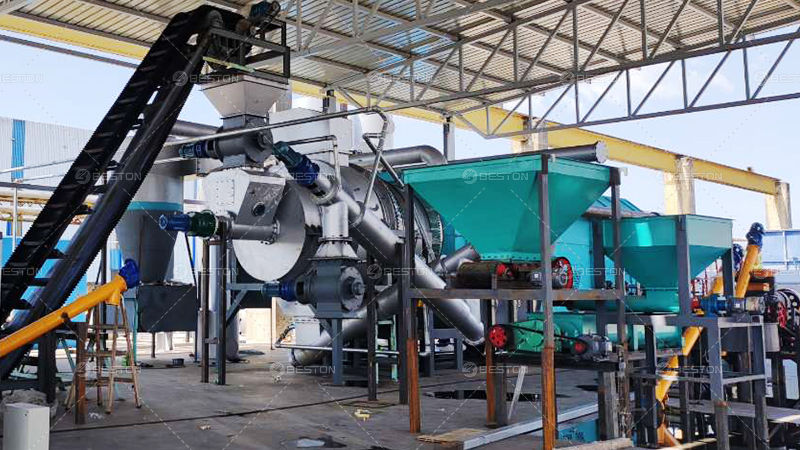
Improving Thermal Efficiency
Effective heat distribution and utilization are critical for ensuring consistent pyrolysis conditions and minimizing energy wastage. Several techniques can enhance thermal efficiency in a carbonization furnace.
Optimized Insulation: High-performance refractory materials, such as ceramic fiber or firebrick linings, can significantly reduce heat loss from the reactor chamber. Enhanced insulation stabilizes internal temperatures and reduces external heating requirements.
Syngas Utilization: The volatile gases released during pyrolysis contain combustible compounds that can be redirected to fuel the reactor. Utilizing syngas as an auxiliary energy source reduces reliance on external fuels and improves overall energy efficiency.
Temperature Uniformity: Uneven heat distribution can lead to incomplete pyrolysis and inconsistent biochar quality. Advanced burner configurations and strategically placed heating zones ensure uniform thermal conditions throughout the reactor chamber.
Feedstock Preparation and Optimization
The characteristics of the biomass feedstock influence pyrolysis efficiency, reactor performance, and biochar quality. Proper feedstock preparation enhances conversion efficiency and minimizes operational disruptions.
Moisture Content Reduction: High-moisture biomass requires additional energy for drying, reducing overall efficiency. Pre-drying biomass to an optimal moisture level (typically below 15%) enhances thermal conversion efficiency and prevents steam-related inefficiencies.
Particle Size Standardization: Uniform particle size distribution improves heat penetration and ensures consistent pyrolysis rates. Biomass with excessively large particles may undergo incomplete pyrolysis, whereas excessively fine particles can lead to excessive gasification. Shredding and sieving feedstock to a uniform size range optimizes heat transfer and reaction kinetics.
Feedstock Blending: Combining different biomass types with complementary characteristics can enhance reactor stability. For example, mixing high-lignin feedstocks with lower-density materials can balance volatile release and improve char structure.
Process Monitoring and Automation
Advanced control systems and automation technologies play a crucial role in optimizing pyrolysis reactor efficiency. Real-time monitoring allows for precise adjustments, ensuring consistent performance and minimizing inefficiencies.
Temperature and Pressure Sensors: Integrating real-time monitoring systems enables operators to maintain precise control over process variables. Automated adjustments to heating rates, feedstock flow, and residence time optimize reactor conditions.
Gas Composition Analysis: Monitoring the composition of emitted gases helps optimize process parameters and improve syngas utilization. Automated gas analyzers can detect fluctuations in volatile compounds, enabling adjustments to combustion or condensation systems.
Automated Feeding Systems: Consistent and controlled biomass feeding prevents fluctuations in reactor temperature and ensures steady-state operation. Mechanized conveyors and metering systems enhance process stability and reduce manual intervention.
Reducing Operational Downtime
Minimizing downtime and maintaining consistent reactor performance is essential for maximizing throughput and profitability. Preventative maintenance strategies and design improvements can reduce the frequency of shutdowns and repairs.
Wear-Resistant Components: Using high-durability materials in reactor construction reduces degradation from prolonged thermal exposure. Alloy steel or ceramic coatings can enhance the longevity of reactor walls and heating elements.
Clogging Prevention Measures: Tar buildup and ash accumulation can obstruct reactor components and hinder performance. Regular cleaning protocols, automated self-cleaning mechanisms, and optimized feedstock selection minimize reactor fouling.
Scheduled Maintenance Protocols: Implementing proactive maintenance schedules ensures that key reactor components remain in optimal working condition. Routine inspections and predictive maintenance technologies prevent unexpected breakdowns and extend reactor lifespan.
Expanding the Value Chain
Beyond optimizing reactor efficiency, maximizing the economic potential of biochar production involves leveraging its by-products and exploring diversified revenue streams.
Biochar Refinement: Upgrading raw biochar through pelletization or activation enhances its commercial value. Specialized processing techniques can tailor biochar properties for agricultural, industrial, or environmental applications.
Liquid By-Product Utilization: The condensable volatiles released during pyrolysis can be refined into bio-oil or specialty chemicals. Efficient condensation and separation systems enhance yield recovery and marketability.
Carbon Credit Opportunities: Biochar serves as a recognized method for long-term carbon sequestration, making it eligible for carbon credit trading. Leveraging biochar’s environmental benefits can open new revenue avenues in carbon markets.
Maximizing biochar pyrolysis reactor efficiency requires a comprehensive approach encompassing reactor design, energy optimization, feedstock preparation, automation, and value chain expansion. Implementing these strategies ensures higher yields, lower energy consumption, and greater economic returns for biochar producers.
Comments