Waste Gas Emission Control in Plastic Pyrolysis
- arbourz
- Dec 26, 2024
- 4 min read
The growing demand for sustainable waste management solutions has made plastic pyrolysis an attractive option for recycling plastic waste. This thermochemical process breaks down plastic polymers into valuable products such as pyrolysis oil, gas, and carbon black. However, like any industrial process, plastic pyrolysis generates waste gases that must be carefully managed to minimize environmental impact. Effective waste gas emission control is crucial for ensuring that plastic to fuel machine operates in compliance with environmental regulations and contribute to the circular economy.
Nature of Waste Gases in Plastic Pyrolysis
During plastic pyrolysis, the raw plastic feedstock undergoes thermal decomposition at elevated temperatures (typically between 350°C and 700°C) in the absence of oxygen. As the plastic melts and breaks down, various volatile compounds are released, including hydrocarbon gases, volatile organic compounds (VOCs), sulfur compounds, and other potentially hazardous substances. These gases can cause air pollution if not properly treated, leading to environmental degradation and health risks.
The composition of waste gases varies depending on the type of plastic being processed. Common plastics like polyethylene (PE) and polypropylene (PP) release different levels of gases, but all pyrolysis reactions produce some combination of methane, ethylene, propane, butane, and carbon monoxide. Additionally, impurities in the feedstock can result in the emission of more complex organic compounds, which may require additional purification steps.
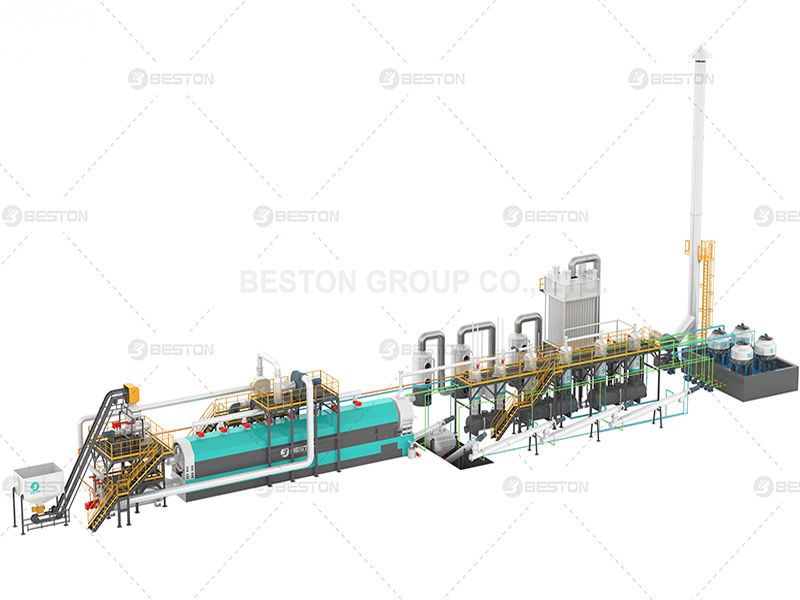
Key Challenges in Waste Gas Emission Control
The main challenge in managing waste gases from a plastic to oil machine is the diversity of substances produced and the potential for harmful emissions. These gases often contain pollutants that, if released unchecked, can contribute to smog formation, acid rain, and health issues such as respiratory problems and eye irritation. Furthermore, the high concentration of carbon monoxide and other harmful gases presents a risk of explosive reactions if not safely contained.
To address these challenges, it is essential to implement advanced gas treatment systems that can effectively capture, neutralize, or convert harmful emissions into non-toxic substances. Additionally, the variation in the composition of waste gases necessitates the customization of emission control technologies to suit the specific characteristics of each plastic feedstock.
Techniques for Waste Gas Emission Control
Several methods are employed to treat and control waste gas emissions in plastic pyrolysis plants. These techniques help ensure that the process remains environmentally friendly and compliant with air quality standards.
1. Thermal Oxidation (Incineration)
One of the most common methods for treating pyrolysis gases is thermal oxidation. In this process, waste gases are subjected to high temperatures in a controlled combustion chamber, where harmful gases are oxidized and converted into less harmful byproducts, primarily carbon dioxide (CO2) and water vapor. Thermal oxidation is highly effective at reducing volatile organic compounds (VOCs), carbon monoxide, and other hazardous substances. However, it requires a substantial energy input, which can impact the overall energy efficiency of the pyrolysis plant.
2. Gas Scrubbing
Gas scrubbing is another essential technique for controlling emissions in a plastic pyrolysis plant. In this process, waste gases are passed through a scrubbing solution, typically an alkaline or acidic liquid, which absorbs or neutralizes harmful compounds. Scrubbing effectively removes sulfur compounds, acidic gases, and particulate matter, ensuring that only clean gases are released into the atmosphere. This method is especially effective for plastics that contain chlorine, such as polyvinyl chloride (PVC), which can release harmful chlorine-based gases during pyrolysis.
3. Catalytic Conversion
Catalytic conversion involves passing the waste gases through a catalyst that facilitates the chemical reaction to break down harmful compounds into less toxic substances. For example, catalysts can convert carbon monoxide into carbon dioxide, a less harmful greenhouse gas. This method is more energy-efficient compared to thermal oxidation, as it operates at lower temperatures and consumes less energy. However, catalytic converters must be carefully selected to match the composition of the pyrolysis gas to ensure maximum efficiency.
4. Activated Carbon Filtration
Activated carbon filtration is an effective method for removing VOCs and other organic pollutants from pyrolysis gas. The process involves passing the gases through a bed of activated carbon, which adsorbs harmful substances, trapping them on the surface of the carbon particles. This technique is particularly useful for removing odors and other trace contaminants, ensuring that the waste gases are cleaner before they are released into the environment.
5. Flare Systems
Flare systems are often employed in plastic pyrolysis plants as a safety measure to handle excess waste gases. These systems burn off unwanted gases that cannot be processed efficiently by other treatment methods. While flaring is not a primary solution for emission control, it can be used in emergency situations or during periods of high gas production, ensuring that potentially dangerous gases are safely incinerated.
The Role of Process Optimization
In addition to installing effective emission control technologies, optimizing the plastic pyrolysis process itself is critical for minimizing waste gas production. Fine-tuning parameters such as temperature, pressure, and residence time can help reduce the formation of harmful gases and increase the yield of valuable byproducts like pyrolysis oil and carbon black. By optimizing reactor design and feedstock preparation, it is possible to enhance the efficiency of both the pyrolysis process and the associated gas treatment systems.
Conclusion
Waste gas emission control in plastic pyrolysis is essential for reducing the environmental impact of plastic recycling operations. By employing advanced technologies such as thermal oxidation, gas scrubbing, catalytic conversion, activated carbon filtration, and flare systems, plastic pyrolysis plants can ensure that harmful emissions are effectively neutralized or reduced. In addition, optimizing the pyrolysis process itself plays a crucial role in minimizing waste gas production and improving the overall sustainability of the operation. As the demand for plastic waste recycling continues to grow, innovations in emission control will remain critical to the success of the industry.
Comments