Waste Pyrolysis Plant Core Components
- arbourz
- Mar 16, 2021
- 2 min read
Continuous waste tire pyrolysis plants are set up worldwide to deal the increasing quantities of global tire waste. Tire pyrolysis is undoubtedly an eco-friendly strategy to recycle scrap tires into usable commodities, such as fuel oil and carbon black. The need for eco-friendly pyrolysis plant design have never been greater. It is true you could see the world's largest tire landfill site in Kuwait from space.
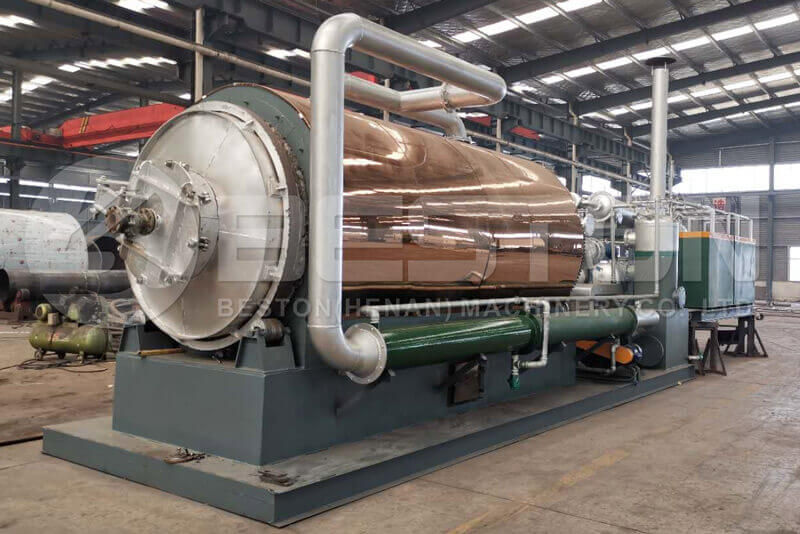
Waste Tyre Pyrolysis Plant Core Components
1. Reactor
The reactor is perhaps the most important component in the tire pyrolysis plants. The two main various kinds of reactors: rotary and fixed. The structure from the first type is such how the reactor can rotate 360-degrees to make sure every area from the reactor are heated evenly. The rotary design enables you to speed up pyrolysis and prolong the service life of the component. A fixed reactor carries a stable design and is not going to rotate. Fixed reactors are employed in fully continuous pyrolysis plants could they be are more energy-efficient than skid mounted tyre pyrolysis equipment that employ a batch working method.
2. Casing
A pyrolysis reactor is covered in a special casing that was designed to retain heat inside the main vessel and reduce fuel costs. Additionally it is employed for isolating oil-based cuttings.
3. Manifold
Vapor from your pyrolysis reactor moves in the manifold, which was designed to separate heavy and light oil. Light oil then rises to another condensing systems while the heavy oil flows into a residual oil tank, Heavy oil containing fine dust is sent back into the reactor with an oil pump for additional refinement.
4. Condenser
The condenser is commonly used to convert the vaporized oil into liquid oil. The tubular design of condensers on top-rated pyrolysis machines make certain that you will find a large cooling area for condensing, which could significantly improve oil yield. What's more, tubular water-cooled condensers are really easy to maintain. See the waste pyrolysis machine UK.
5. Dedusting System
The dedusting system is composed of three layers of exhaust cleaning components to make certain there is not any pollution in the plant's emissions. Three of the layers including water washing, ceramic ring adsorption, and water spray. The de-dusting method is key to ensure tire to oil machines meet strict environmental protection regulations.
The 5 components outlined above are just some of the most key components that comprise a pyrolysis plant. The fifteen main aspects of a normal waste tire pyrolysis oil plants are reactor, casing, heavy oil tank, manifold, oil condenser, hydroseal, carbon discharger, oil tank, burning room, gas gun, air blower, flue condenser, water tank, cooling tower, and dedusting system. Depending on the manufacturer, the design of a plant can usually be completely customized to meet the unique specifications of the buyer.
You will find batch, semi-continuous, and fully-continuous designs available. The kind of plant design a buyer opts for will depend on the amount of tires that require to process per week and space they have designed for machinery with their facility. Budget restraints could also obviously affect the particular plant design accessible to tire recycling facility operators. Get the machine to make oil from old tyres.
Comments